
建設機械
株式会社小松製作所 コマツが推進する「設計プロセスの再設計」2022.04.08
デジタルで技術・ノウハウの伝承を推進
「タテ」と「ヨコ」のデジタル化によって、スマートコンストラクションを強力に推進している株式会社小松製作所(コマツ)。ここでは製品設計のプロセスも、同様の考え方で改革しています。しかし、その道筋は決して一筋縄ではありませんでした。設計者自身が設計プロセスを「設計し直す」ことは、予想外に困難でした。そこで、同社はプログレス・テクノロジーズ(PT)を活用することで、設計プロセス改革を大きく前進させることができました。
APPROACH
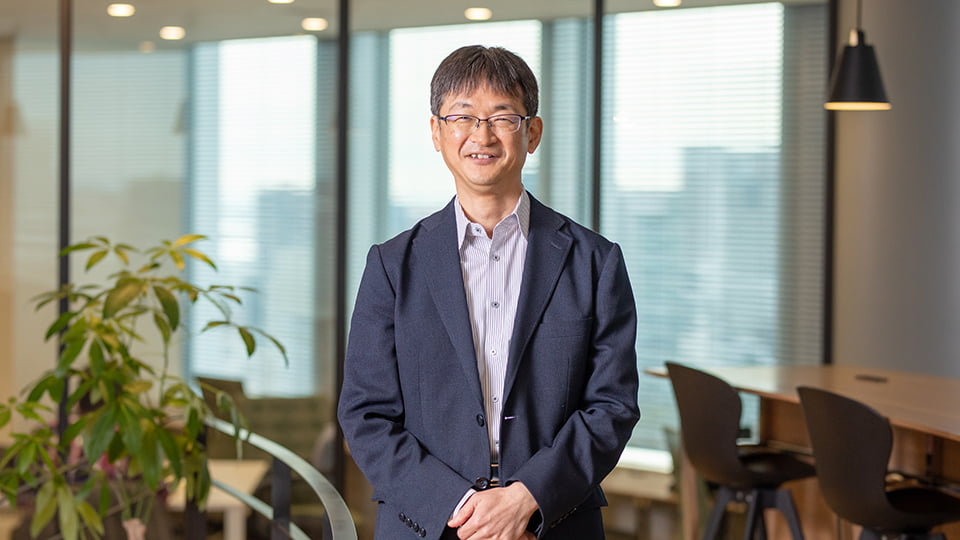
ベテラン頼みから脱却するため設計プロセスの改革へ
ICT建機による建設機械の自動化を起点としたスマートコンストラクションによって、オペレーターの高齢化や人材不足をはじめとする建設現場の様々な課題解決に取り組んでいるコマツ。個々の施工プロセスをデジタル化する「タテのデジタル化」だけではなく、全プロセスがデジタルによって繋がる「ヨコのデジタル化」も行うことで、施工全体の最適化を推進しています。その考え方は、自社製品の設計業務にも活かされています。同社では建設機械の性能の決め手となる様々な機器を自社開発していますが、その設計プロセス改革も着々と進められています。
その背景について、コマツ 開発本部 油機開発センタ 先行研究グループでGMを務める 名倉 忍氏は、次のように語ります。「設計部門には複雑化・多様化する製品要求に対し、高品質でタイムリーな開発を行うことが求められています。しかし私が所属する油機(※1)開発部門では、1980~90年代の成長期を支えてきた経験豊富なベテラン技術者が高齢化しており、その技術・ノウハウをどのように伝承していくかが大きな課題になっていました。設計時に何を検討し、どの情報を参照するかは暗黙知の部分が大きく、その多くをベテラン設計者の経験に頼っていました。社内には設計時に参照すべき膨大な情報があるものの、効率的に参照できないことも属人的な設計プロセスの要因になっていました」
この問題を解決するため、油機開発センタは設計プロセスの改革プロジェクトに着手。これはまさに「設計業務を設計し直す」取り組みですが、当初はなかなかうまく進まなかったと振り返ります。「設計者は日々の設計業務に忙殺されており、プロセス改革に費やせる時間が限られています。その上、すでに慣れてしまっている設計プロセスのどこに課題があるのか、自分たちでは気づけないという問題もありました」(名倉氏)
他社とは大きく異なっていたPTのコンサルティング
このような状況に風穴を開けたのが、PTによるコンサルティングです。
「とある企業からPTはの紹介を受けたのがきっかけです」と名倉氏は語ります。そこでPTの取締役CTOでコンサルタントでもある長友一郎と話をする機会を設けたところ、「設計あるある」的な話題が数多く出てきたのだといいます。「このような人が外部から参加すれば、設計プロセスを再設計するといったことも、可能になるのではないかと考えました」(名倉氏)
名倉氏は、他の会社のコンサルタントとも話をしていましたが、PTのコンサルタントは他の会社とは大きく異なるところがあったと指摘します。1つは話している言葉です。コマツの設計者が使う言葉で話をしてくれるため、聞いていて違和感がなかったと話します。もう1つは仕事に対するスタンスです。PTの提案は、設計者と同じ立場で解決策を探るという点が特長的で、設計現場にしっかり入り込んだものでした。
「設計プロセスの課題を解決していくには、設計現場の状況を聞いて把握する必要がありますが、そこでPTが行ったのはもはやヒアリングといったレベルではありませんでした。まず設計者の言葉で話をして、設計者をとことん理解した上で、設計者自身と意識を合わせていったのです。自分たちのことをわかってくれる人には、設計者も本当のことを話したくなるものです」(名倉氏)
PTのコンサルタントはコマツに常駐しながら、この取り組みを推進。油機開発センタが抱えている様々な課題をあぶり出していきます。そのうえで、同社が「PT DBS(Design Basis Solution)」と呼ぶ独自の方法論を活用し、ベテラン設計者が持つ設計手順や知見などの暗黙知を、デジタルデータとして可視化していきました。
例えば設計検討計画段階で行われるFMEA(※2)では、次のようなプロセス改革が実現されています。
設計ナレッジをデジタル化し、懸念事項の抜け漏れを回避
従来の設計方法では、個々の設計者が頭の中のノウハウを用いてFMEAを行い、その上で設計図面を作成していました。ここで懸念事項の抜け漏れが見つかった場合には、再びFMEAへと戻ります。ベテランが行う場合には比較的少ない手戻りですみますが、経験が少ない設計者では膨大な手戻りが発生する可能性があります。またデザインレビュー時にベテラン設計者が新たな懸念事項を発見し、大きく手戻りすることも少なくありません。このような手戻りを多くの設計者が「品質の作り込み」だと考えていましたが、これが設計期間の長期化や、設計品質のばらつきに繋がっていました。
その解決のためにまず行われたのが、既存資料の情報をリスト化し、どこに参照すべき情報があるのかを明確化することでした。次にベテラン設計者の知見を追加することで情報を補充。さらにベテラン設計者の知見による情報同士の紐付けも行われました。
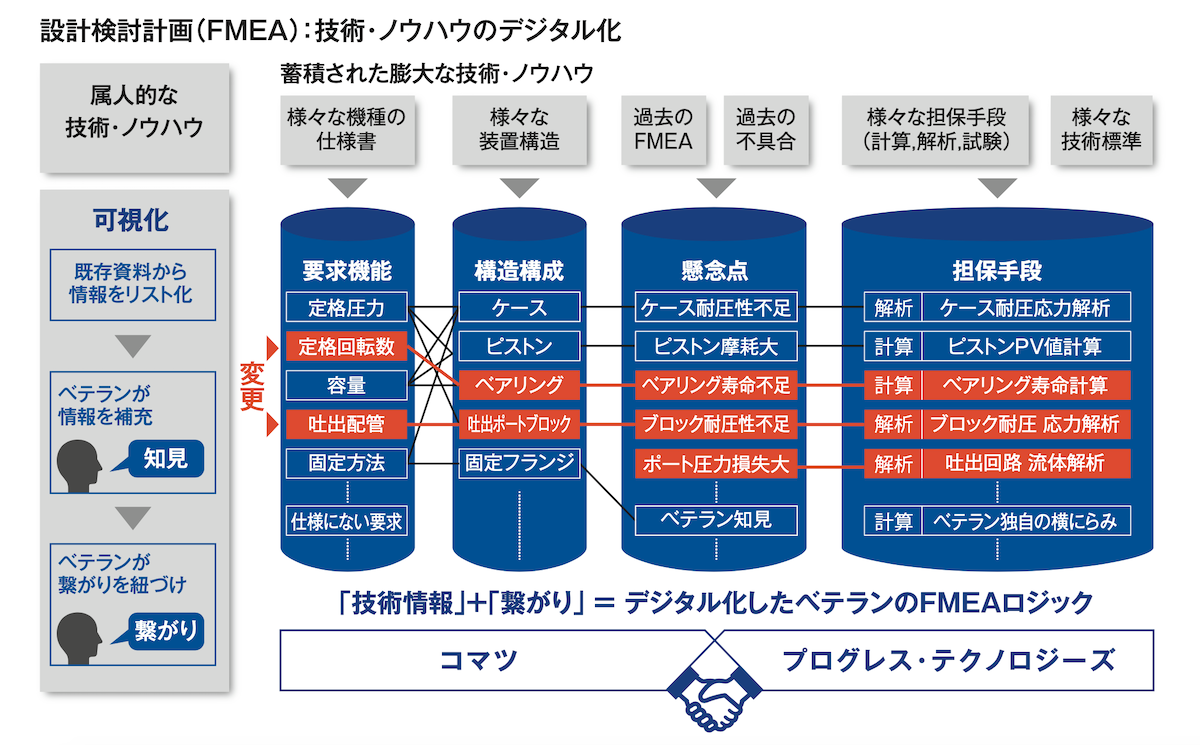
例えば要求仕様の変更に伴い定格回転数の変更が必要な場合、その影響はベアリングにも及び、ベアリングの寿命不足が懸念されます。そこでFMEAではベアリング寿命計算を行い、そのリスクを評価しなければなりません。これら一連の流れと参照すべき情報の繋がりを意識しながらデジタルで可視化することで、FMEA時の抜け漏れを排除しました。
また、設計時に得られた新たな知見は、そのまま設計ナレッジとして登録されるようになっています。もちろんデザインレビュー時の新たな指摘も、ナレッジに反映されます。
地道なコミュニケーションで、設計者自身の”自分ごと”に
このような改革を実現するには、ベテランを中心とした設計者の巻き込みが欠かせません。その具体的な取り組みは、次のように進められました。
まずベテラン設計者やグループマネージャとの地道なヒアリングを繰り返し、課題を深堀りした上で解決の方向性をすり合わせ、基本方針を明確化。次に若手設計者が感じている課題についても調査が行われました。さらにこれらの情報をまとめ上げて試験的な環境を構築し、中堅以上の設計者が「デジタル化された設計プロセス」を体感。具体的なイメージをつかんでもらった上で、本格的なプロセス改革のための活動が展開されました。
「ここで重要なのは、設計者が ”腹落ち” して ”自分ごと” にすることです。そこに至るまで、地道なコミュニケーションを徹底的に繰り返しました。その結果、設計者自身が改革マインドになり、主体的で力強い活動になったのです。ここで大きな役割を担ったのがPTのコンサルタントです。社内だけで取り組んでいたら、これだけ力強い活動にはなっていなかったと思います」(名倉氏)
すでにFMEA以外にも、ポンプの基本設計などで改革が進んでいると名倉氏は話します。これにより、毎日忙殺されて将来に対しても漠然と抱えている設計現場の不安に、明るい兆しが見えてきていると言います。
「若手設計者にとってベテランに話を聞くのは気が重いものですが、自分で簡単に調べられるようになったことで、自立的に知見を増やせる ようになりました。これら設計プロセス改革は、設計者のモチベーション向上にも寄与していると考えています」(名倉氏)
将来展望として、名倉氏は次のように語ります。「最終的に目指すのは、部門横断型の設計DXを実現し、それをスマートコンストラクション等のサービスを通して得られるデータと横のデジタル化で繋いでいくことです。このようなコマツならではの設計プロセスを実現し、社会やお客様の期待に応えていける商品の継続的な開発に活かしていきたいと考えています」
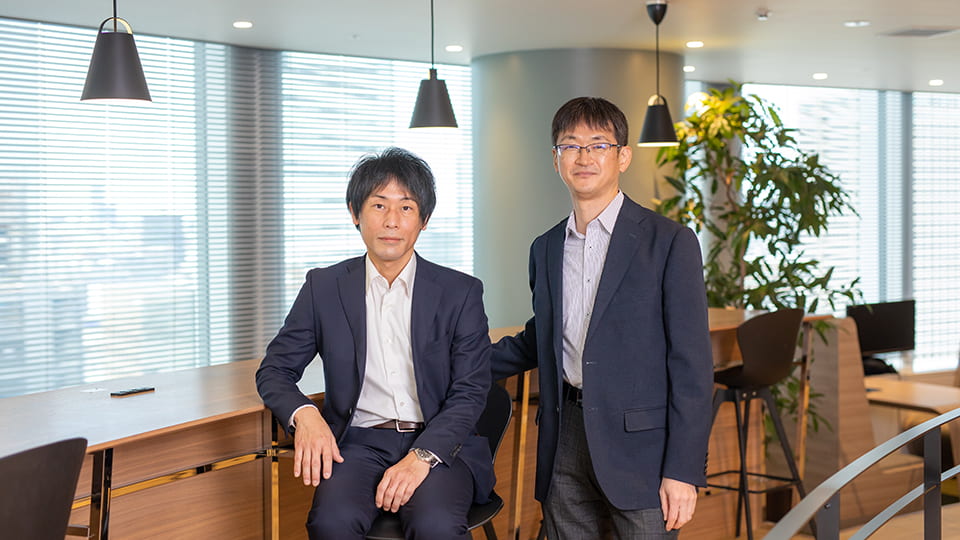
設計プロセスの再設計を推進したコマツの名倉忍氏(右)とプロジェクトを支えたプログレス・テクノロジーズの長友一郎(左)
関連するサービス
MEMBER
プロジェクトに関わったメンバー
CASES
プログレステクノロジーズの
ソリューション事例
ソリューション事例